【典型案例】格力协同制造长沙商用空调智能工厂工业网络实施情况
2021-02-10 来源:智造苑
「 1. 工厂网络布局 」
长沙格力暖通制冷设备有限公司(简称“长沙格力”)从规划开始,结合自身生产制造情况,不断投入大量精力对工业网络分步实施建设,实现园区内关键设备100%实现互联互通,将人、数据及智能设备运用专业工厂管理软件通过集团网络互联,在确保信息安全的前提下,实现效率提升、降低成本、减小资源使用的目标。其网络架构具有如下特点:
(1)全面性:园区内5大车间,3大库房有线网络和无线网络无死角全覆盖,为设备联网提供了保障;
(2)高效性:系统网络主干万兆,千兆到桌面,实现虚拟化、桌面化;长沙格力到珠海格力电器总部由40M电信专线与10M联通专线组成,保证了集团内的互联互通。
(3)灵活性:系统采用标准的传输线缆和相关连接硬件,模块化设计,所有通道都是通用的,所有设备的开通及更改均不需改变布线线路,并可灵活多变组网。
(4)可靠性:系统采用高品质的材料和组合压接的方式构成一套高标准的信息传输通道,应用系统应采用点到点端接,任何一条链路故障均不影响其它链路的运行,从而保证整个系统的可靠运行。
(5)安全性:内部网络物理隔离,采用加密这种主动的防卫手段保障内部网络系统安全 。
「 2. 数字化设备选型 」
长沙格力在设备规划初期广泛选取了数字化、自动化设备,设备是可感知的且具备一定数据处理能力,能够实时采集设备动态的运行数据,并根据预置的模型自主选择要回传到远程地点进行分析和存储的数据。另一方面,机器是数控可编程的,能够根据自身传感的反馈或远程发送的数字指令执行相应动作。
面对不同厂商的设备PLC接口、协议不同,提前约定了标准,最大程度上统一了通讯接口、类型、协议,为设备互联互通奠定了基础。
「 3. 各类标识技术的应用 」
通过条码、RFID信息化技术实现了原材料来料批次化管理,生产订单定额领料,生产流水线的每个工序的生产状况以及在生产过程中数据操作的准确化和系统化,建立产品生产控制跟踪;实现从成品到半成品到部件、零件、原材料的可监控可追溯性;从而完成产品生产的内部流程追溯管理及外部进出的源头追溯和质量数据管理。
(1)来料条码批次化管理,通过无线网络将手持终端扫描条码信息实现系统入库,出库数据的同步;实现实物流和信息流的一致; 现场人员可通过手持终端查询货物的数量、存放位置、批次等信息;提升仓库管理质量和提高工作效率。避免了人工录入数据,提高了数据的准确性。
(2)生产过程的全程监控透明化管理,通过MES系统在产品上线时绑定RFID标签,建立生产批次跟RFID标签关联关系,记录、跟踪生产过程的工序生产环节,产品能够追踪到生产中的哪道工序、哪些物料、哪个机型、哪些生产班次人员等等存在的问题。
(3)成品库位精细化管理,通过自动设备堆板扫描条码标识,能节省成品入库、移库、发货工作量,保证成品库存信息的准确性、高效性,在移库过程中通过条码标识跟库位的绑定,实现成品库位精细化管理,能快速、准确的实现产品位置定位。
「 4. ERP和MES系统的深度融合应用 」
在格力目前的生产管理过程中,计划与资源管理以ERP为核心,制造现场以MES业务架构为核心,围绕两大平台的融合应用,格力电器自主研发了以ERP下达生产计划为依托,MES现场采集数据做拉动的制造信息协同管理平台,实现了工厂软件之间的横向互联、数据流动、转换和互认,两大系统数据同步率达到100%,实物流和信息流的高度一致。
通过该平台的应用,将ERP的计划管理和MES的现场管理进行了深度融合(图1)。平台的主要功能模块分为以下三个:
(1)通过齐套排产管理系统实现了生产计划与物流协同;
(2)通过电子拣选系统(SAM)实现了配送计划与线边需求协同;
(3)通过落地反冲系统实现了执行过程与账务管理协同。
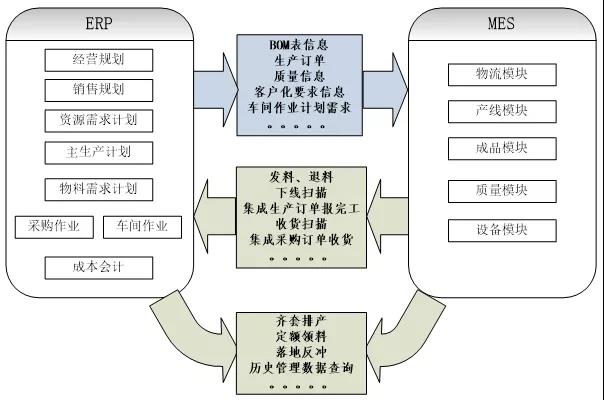
图1 ERP和MES系统的深度融合
「 5. 工业网络实施后效果 」
长沙格力工厂基于SCADA系统平台搭建工业网络的软件架构(图2),最底层为车间设备层,通过的IGS接口软件同设备层的PLC连接,采集设备运行的实时数据;同时将实时数据传入iHistorian实时数据库,部分生产统计数据也会通过iHistorian导入关系数据库,数据在数据库层进行处理和存储;再上一层为SCADA核心应用层,该层通过iFix软件开发并展示生产过程监控、设备呼叫报警及生产订单管理的相关应用业务;通过SCADA与MES的接口层与格力MES系统进行接口,一方面可以从MES层接收MES排好的生产订单,同时会将生产订单的执行完成情况反馈给MES系统,另一方面通过接口层也可以给MES反馈MES所需要的设备生产运行的一些实时数据,如设备故障报警等信息,以供MES根据生产现场的实时信息做出相应的处理。
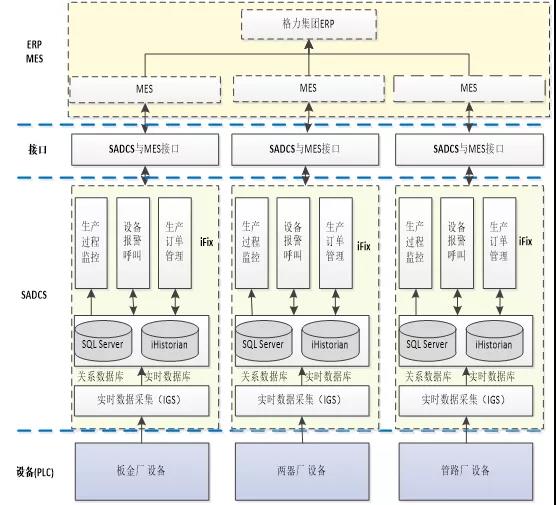
图2 工业网络的软件架构
长沙格力应用了传感器、仪器仪表、条码、机器人等感知技术,通过可编程逻辑控制器(PLC)、数据采集与监视控制系统(SCADA)控制,实现了各分厂100%的关键设备互联互通,实时采集设备的动作、状态信息,大量减少了人工采集生产过程数据的操作,降低公司运营成本,形成效果要点如下:
(1)实现5大车间关键设备100%互联互通;
(2)实现设备运行状态的实时采集;
(3)有效降低了设备管理和数据采集的人力资源投入;
(4)提高设备异常的响应速度;
(5)数据深度挖掘与应用。
通过管理数据平台的整合,将公司的数据存储集中在公司层面的平台中,并且实现数据存储位置的互通,建立起公司生产制造管理的大数据库,通过云计算、数据挖掘等手段,实现关键指标和过程控制异常的自动分析提醒、集控管理。从而提高公司运作的信息融合度,形成效果要点如下:
(1)建立起了集中管理的公司级生产过程大数据平台。
(2)运用IFIX软件进行组态编程,构建设备现场的虚拟模型,实现工厂数字化远程管理功能。
(3)建立了可靠性高、毫秒级读取速度的数据库,保证工具系统的快速应用。
(4)实现生产数据的自动分析,形成公司级生产决策平台。
相关新闻
版权声明
1、凡本网注明“来源:中国轻工业网” 的作品,版权均属于中国轻工业网,未经本网授权,任何单位及个人不得转载、摘编或以其它方式使用。已经本网授权使用作品的,应在授权范围内使用,并注明“来源:中国轻工业网”。违反上述声明者,本网将追究其相关法律责任。
2、凡本网注明 “来源:XXX(非中国轻工业网)” 的作品,均转载自其它媒体,转载目的在于信息之传播,并不代表本网赞同其观点和对其真实性负责。
3、如因作品内容、版权和其它问题需要同本网联系的,请于转载之日起30日内进行。
4、免责声明:本站信息及数据均为非营利用途,转载文章版权归信息来源网站或原作者所有。