智能制造的核心技术之建模与仿真技术
2022-03-09 来源: 智造苑
「 1. 建模与仿真技术的定义 」
建模与仿真技术从严格意义上说,是两个技术的复合名词,即建模技术与仿真技术。建模是仿真的基础,建模是为了能够进行仿真。仿真是建模的延续,是进行研究和分析对象的技术手段。
具体到智能制造中,建模技术是指,针对制造中的载体(如数控加工机床、机器人等)、制造过程(如加工过程中的力、热、液等问题)和被加工对象(如被制造的汽车、飞机、零部件),甚至是智能车间、智能调度过程中一切需要研究的对象(实体对象或非实体化的生产过程等问题),应用机械、物理、力学、计算机和数学等学科知识,对研究对象的一种近似表达。
仿真技术是在建模完成后,结合计算机图形学等计算机科学手段,对模型进行图像化、数值化、程序化等的表达。借助仿真,可以看到被建模对象的虚拟形态。
「 2. 建模与仿真技术的特点 」
从需求本身出发,建模与仿真技术表现出以下特点:
(1)虚拟化:虚拟化是建模与仿真技术的最本质特点,利用建模与仿真技术可得到被研究对象的虚拟镜像。
(2)数值化:数值化是建模与仿真技术的必要特点,是仿真、计算、优化的前提。
(3)可视化:可视化是建模与仿真技术的直观特点,是建模与仿真技术人机交互与友好性的体现。在智能制造中,可视化几乎是一切建模与仿真技术所共有的特点和属性。可视化可以帮助科研人员直观分析被研究对象的动态行为,也可以帮助车间技术人员快速掌握加工过程或加工对象的实时状态。
(4)可控化:可控化是建模与仿真技术通往终极目标的必要手段。建模与仿真技术的目的是对被研究对象进行分析和优化。只有在建模与仿真技术中做到可控化,才可以进行科学化的对照试验、优化试验等。
建模与仿真技术的特点随着制造业的发展而不断更新。
另外,随着制造业的转型升级,从传统制造到数字制造,从数字制造到数字化网络化制造,再到数字化网络化智能化制造,建模与仿真技术又表现出一些新的特点:
(1)集成化:智能制造发展的初级阶段,即数字制造,制造对象或制造主体(机床或机器人等)主要表现出单元化的制造特点;到了智能制造发展的第二阶段,即数字化网络化制造,制造对象或制造主体又表现出在互联网下的多边互联特点;再到数字化网络化智能化的第三阶段,依托5G、物联网、云计算、云存储等技术,实现各制造对象或制造主体之间的互联互通,人-机-物的有机融合,建模与仿真技术也从原来的单一化过渡到多机协同的集成化模式。
(2)模块化:模块化似乎是与集成化相悖的一个概念和特点,但其实不然。数字化制造过程中,由于加工对象单一,加工过程单一,建模与仿真技术也表现出模型与实体对象的一一对应的特点。但到了智能制造发展的第三阶段,由于加工过程更为复杂,加工对象更多,各个对象之间还有紧密的联系,建模与仿真技术也变得更复杂,更有必要在复杂的条件下构建模块化的建模单元与仿真单元,以便不同人员跨地区、跨学科、跨专业、跨时段地进行协同建模与仿真开发。
(3)层次化:HLA(high-level architecture)是智能制造中的一个代表性的开放式、面向对象的技术架构体系。在HLA架构体系下,智能车间、智能工厂、智能仓储、智能化嵌入式系统、智能化加工单元等作为智能制造网络化体系结构的下端级,云平台、云存储作为上端级,边缘计算、云计算作为沟通中间的连接驱动和计算资源。针对复杂网络体系下的智能制造,需要更加层次化的建模与仿真,有利于模型的管理、重用、优化升级与快速部署。
(4)网络化:5G是智能制造时代的高速信息通道,智能制造与5G技术的结合,更有利于将人-机-物进行有机融合,各加工制造单元互联互通,模型交互与模型共享,仿真数据共享。
(5)跨学科化:智能制造生产活动中,表现出了多学科和跨学科的特点。建模与仿真技术在集成式发展的过程中,也表现出集机械、电磁、化学、流体等多学科知识,表现出多专家系统模式。典型的如CAM软件,既能够进行机械的三维实体建模,又能对模型进行有限元分析、流体分析与磁场分析等。
(6)虚实结合化:虚实结合化是智能制造中建模与仿真技术的重要特点,也是前沿方向。典型的如VR(virtual reality)、MR(mixed reality)、AR(augmented reality)等技术,这些技术的共同特征都是能让人参与虚拟化的建模与仿真技术,与实体对象进行交互,增强仿真过程中的真实体验。
(7)计算高速化:随着计算机技术和网络技术的快速发展,能够对制造活动中的对象进行越来越真实的建模与刻画,仿真过程也越来越丰富。虽然模型的计算复杂度大幅度提升,但依托于高速计算机、大型服务器、高速总线技术、网络化技术和并行计算模式,建模与仿真也表现出计算高速化的特点。计算高速化的建模仿真,是虚拟化模型与实体制造加工过程进行实时协作的关键技术。高性能计算(HPC)利用并行处理和互联技术将多个计算节点连接起来,从而高效、可靠、快速运行高级应用程序。基于HPC环境的并行分布仿真是提高大规模仿真的运行速度的重要方法。
(8)人工智能化:传统的建模仿真主要是三类,即基于物理分析的机理模型、基于实验过程的经验推导模型、基于统计信息的统计模型。智能制造是一个高度复杂和强耦合的体系,传统的模型在一些要求较高的条件下,往往并不能满足需求。而通过借助人工智能技术,如人工神经网络、核方法、深度学习、强化学习、迁移学习等对非线性强耦合的加工过程和加工对象进行建模,能够得到传统建模方法达不到的精准效果。
(9)数据驱动化:工业大数据是数字-智能时代工业的一个伴生名词,工业大数据指智能制造活动中,加工实体、加工过程等一切参与智能制造活动的对象所产生的数据资源。工业大数据背后往往隐藏着巨大的制造活动奥秘,而这些奥秘是传统建模与仿真凭借机理推导、单一数据实验和统计难以发现的。基于工业大数据和机器学习技术,能够为复杂制造对象与过程进行建模,并伴随数据量的逐渐累积,所建立的模型与仿真也更加贴合实际。
「 3. 建模与仿真技术的技术体系/关键技术 」
1)建模/仿真支撑环境
建模/仿真的支撑环境是进行建模与仿真的基础性问题。在计算机、网络、软件(管理软件、应用软件和通信软件)、数据库、图形图像可视化的基础上构建建模/仿真支撑环境。建模/仿真支撑环境是建模和进行仿真试验的硬软件环境,它的体系结构应根据仿真任务的需求和规模从资源、通信、应用3个方面来设计,建立适合本应用领域的建模/仿真支撑环境。建模/仿真支撑环境可划分为建模开发环境和仿真运行环境,两者有共享的资源。研究开发环境主要用于建模、仿真系统设计、仿真软件开发等,没有严格的时间管理要求,但要保证事件发生的前后顺序;而仿真运行环境用于仿真系统运行,必需有严格的时间管理,保证实时性。一般情况下,仿真系统运行时调用的资源是固定的、静态的,要实现调用动态资源则建模仿真环境体系结构更复杂。在智能制造的背景下,建模/仿真技术的支撑环境也越来越复杂,从单计算机平台,过渡到多机协同建模与仿真平台,从个人电脑迁移到云端进行建模与仿真。然而,每一次建模与仿真技术的革新,往往伴随支撑环境底层技术的突破。
2)先进分布仿真
从单元化制造到集成化网络化制造,也呈现出分布式建模与仿真的新模式。基于仿真的设计、基于仿真的制造涉及多个专业、多个单位,他们可能分布在不同地区,应将分布在各地理的仿真系统、模型、计算机、设备,将通过网络构成分布联网仿真系统。仿真运行时,仿真系统中的模型之间,计算机之间,仿真系统之间有大量数据和信息传送和交互。
美国国防部于1998 年正式提出基于仿真采办的概念,其两大关键是:
(1)协同环境-协同环境是由互操作的工具和数据库,权威的信息资源,以及产品/过程模型支持的各领域专家可协同工作的环境;
(2)分布产品描述-分布产品描述是数字化产品信息的分布集合,通过 Web 技术互联,对用户呈现单一的逻辑上统一的产品描述,包括产品数据,产品模型,过程模型等。
3)仿真资源库
仿真资源库是仿真技术的依赖性技术。仿真资源库包括数据库,模型库,工具软件库等。仿真系统的开发和运行要用到大量数据和模型,例如飞行器动力学模型和气动数据,全球导航台数据,综合自然环境模型和数据,产品性能的模型和数据,人的行为模型和数据、仿真结果数据等。此外,仿真资源库越丰富,能开展的仿真活动也更为多样。在智能制造中,人是一项关键的因素,将人纳入建模与仿真环境进行协同仿真,是对建模与仿真平台的又一大挑战。因此,建模与仿真技术不但需要有丰富的图形图像仿真资源库、数值计算与数值优化资源库,也要包含语料资源库、音频资源库,甚至是触觉资源库与多专家系统知识库。
4)图形图像综合显示技术
图形图像综合显示技术一直都是建模与仿真技术的关键核心技术,也是最根本的一项技术,是计算机图形学、数据处理等基础技术的综合应用。智能制造对建模与仿真的图形图像综合显示技术提出了更多新的要求,即不但能在单机上进行二维和三维图形显示,更需要满足嵌入式系统仿真过程中的快速在线实时三维显示。这种综合显示技术不再是单一加工对象或加工主体的图形图像化显示,更提出了新的要求,即融合人和加工环境等的仿真显示技术。
数控加工仿真是利用计算机图形学的成果,采用动态图的真实感形式,模拟数控加工全过程。通过数控加工仿真软件,能判别加工路径是否合理,检测刀具的碰撞、干涉,优化加工参数,减低材料消耗和生产成本,最大限度地发挥数控设备的利用率,如图1所示。一个完整的数控加工仿真过程包括:
(1)NC代码的翻译及检查;
(2)毛坯干涉及零件图形的输入和显示;
(3)刀具的定义及图形显示;
(4)刀具运动及毛坯切屑的动态图形显示;
(5)刀具碰撞及干涉检查;
(6)仿真结果报告,包括具体干涉位置及干涉量。

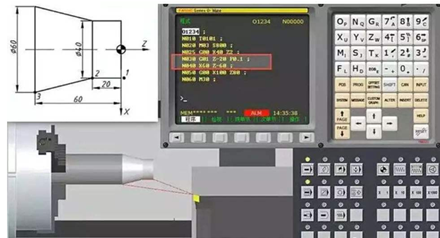
图1 模拟数控加工全过程
「 4. 建模与仿真技术在智能制造中的典型应用案例 」
1)建模与仿真技术在工业机器人中的应用
作为智能制造中的典型应用范例,建模和仿真技术对于机器人的理论研究、设计开发、数据分析、快速产线部署、程序编制、运动规划等都极为重要,更是实现智能制造中加工工艺优化、加工质量与产品性能提升、无人化工厂的关键核心技术。
机器人的建模包括运动学建模、动力学建模、力与环境的物理交互建模等,建模是控制和仿真的基础。典型的运动学建模仿真平台有MATLAB、Gazebo、V-REP等。其中,MATLAB可为机器人进行理论计算研究(如图2所示)。基于其强大的矩阵运算工具箱,研究人员能灵活、方便地进行运动学和动力学建模等。另外,基于Simulink工具箱,还可进行与机器人运动控制相关的实验设计和分析。
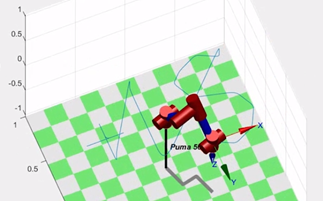

图2 MATLAB机器人运动仿真[38]
Gazebo是一款3D动态模拟器,能够在复杂的室内和室外环境中准确、有效地模拟机器人群。Gazebo可提供高保真度的物理模拟和一整套的传感器模型,还能提供用户和程序非常友好的交互方式。基于Gazebo动态模拟器,可以对机器人算法进行测试,设计机器人和现实场景进行回归测试。一般情况下,Gazebo会运行在Ubuntu操作系统上的 ROS(robot operating system)环境中进行集成使用,如图3所示。
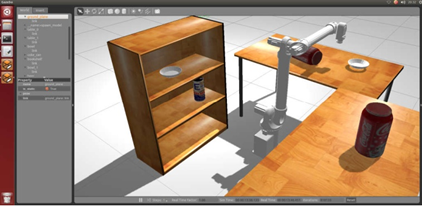
图3 ROS系统下的机械臂运动规划
2)建模与仿真技术在汽车设计中的应用
在现代汽车设计过程中,汽车性能的设计优化主要是利用建模与仿真技术对汽车性能进行预测评估后,根据仿真结果对整车设计参数进行优化。仿真技术使所设计的车型能在不制造出样车、不进行实车试验的情况下,完成对新车型性能的预测和整车设计参数的优化。与传统的汽车性能优化过程相比,仿真技术的应用,缩短了新车型的设计周期,节约了新车型的设计经费,并改进了新车型的性能、质量和成本,这是一种适应人们对新车型要求不断提高的最有效的方法。为此,各大汽车公司在进行新车型开发时,都广泛地应用了建模与仿真技术。
3)建模与仿真技术在制造车间设计中的应用
一般可以把车间的设计过程分为两个主要阶段:初步设计阶段和详细设计阶段。初步设计阶段的任务是研究用户的需求,然后由此确定初步设计方案。详细设计阶段的主要任务是在初步设计的基础上,提出对车间各个组成单元的详尽而完整的描述,使设计结果能够达到进行实验和投产决策的程度,具体来说即确定设备、刀具、夹具、托盘、物料处理系统、车间布局等。而仿真技术则主要用于方案的评价和选择。在初步设计阶段,可以在仿真程序中包含经济效益分析算法,运行根据初步设计方案所建立的仿真模型,对以下信息进行评价:新车间中生产的产品类型和数量能否满足用户要求,产品的质量和精度是否能够满足要求,新车间的效率和投资回收率是否合理。在详细设计阶段,使用仿真技术可以对候选方案的以下方面做出评价:在制造主要零件时,车间中主要加工设备是否能够得到充分的利用,负载是否比较平衡,物料处理系统是否能够和车间的柔性程度相适应,新车间的整体布局是否能够满足生产调度的要求,是否具有一定的可重构能力,在发生故障时,车间生产系统是否能够维持一定程度的生产能力。
「 5. 建模与仿真技术的发展趋势 」
智能制造从单元化,过渡到集成化,再到网络化智能化,建模与仿真技术也呈现出新的技术特点和技术应用。总的来说,伴随智能制造发展的脚步,建模与仿真技术将会更加紧密地与5G、云计算、大数据、人工智能相结合。建模与仿真技术正呈现出实时化仿真、分布式嵌入式仿真、云端建模与仿真、多端建模与仿真和模型资源共享、虚实结合的建模与仿真、人与加工过程参与建模与仿真互动、大数据驱动的混合建模、人工智能和群体智能优化技术结合的建模与仿真等趋势。
随着制造业的发展,建模仿真技术将发挥更加重要的作用。与此同时,由于智能制造系统的新的特点,对仿真技术提出了更高的要求。
1)新一代数字模型
新一代数字模型是将传统的建模仿真技术与新一代的信息技术,如物理信息系统、物联网、大数据、云计算、虚拟现实/增强现实、人工智能等技术相结合,根据特定的需求而构建伴随被建模的物理实体全生命周期、可持续演化且高度可信的数字化模型。新一代数字模型不仅可以进行离线的分析与预测,还能在线地与物理系统进行实时互动。新一代数字模型技术将成为支持新一代智能制造的关键技术之一。
数字孪生技术是一种典型的新一代数字模型技术。它是传统虚拟样机技术的延伸和发展。
虚拟现实(VR)/增强现实(AR)/混合现实(MR)技术也是新一代数字模型技术的重要内容。通过VR可以增加虚拟模型的沉浸感,而AR及MR技术可以实现人、信息系统和物理系统的融合仿真。AR可将计算机生成的虚拟景象叠加到现实景物上,实现人与虚拟物体的实时交互。
制造过程是一个人、信息、机器、环境高度融合的系统。仿真技术除了建立产品模型以及制造所需要的资源、设备、环境等模型外,还可以建立人员的模型。通过人员模型与设备及环境模型的交互式仿真,实现更真实可信的仿真过程。
2)面向制造全生命周期的模型工程
数字模型的建立与管理是制造企业实现制造系统数字化的重要基础。由于制造过程的复杂性,制造生命周期的数字模型拥有一些新的特点。
(1)模型的组成更复杂。模型的组成元素越来越多,元素之间的关系更加复杂。
(2)模型的生命周期更长。智能制造系统中的模型将参与产品的整个生命周期。由于模型元素之间关系的复杂性,模型的演化过程将会非常复杂且呈现高度不确定性。
(3)模型具有高度异构性。大量的模型是由不同的机构采用不同的平台、结构、开发语言和数据库来构建。
(4)模型的可信度极难评估。由于对模型的依赖性的增强,模型的可信度问题也变得越来越重要。由于模型的复杂度增加,评估模型的可信度变得更加困难。
(5)模型的可重用性。为了提高模型开发的效率与质量,模型重用的作用和价值变得更加重要。
综上所述,迫切需要一种面向复杂制造过程全生命周期的模型理论和方法。
3)云环境下的智能仿真技术
随着云计算技术的发展,在制造领域应用云平台技术也逐渐成为一种趋势。在云平台上进行相关制造活动是制造企业进行升级和转型的重要手段。如何在云环境下,通过仿真支持制造全生命周期的协同优化,成为仿真技术面临的新挑战。基于云的仿真技术与智能制造的结合将成为制造系统仿真发展的必然趋势。
4)面向大数据的仿真技术
由于制造系统的复杂化,在制造的全生命周期内产生大量的数据。大数据的出现对仿真技术带来了新的机遇,同时仿真技术对制造大数据的获取、处理、管理和使用也将发挥重要作用。一方面,大数据可以对仿真建模提供新的途径和方法。由于制造系统的高度复杂性,导致采用传统方法对复杂系统建模非常困难。而利用系统运行产生的大量数据样本,通过机器学习的方式可以建立逼近真实系统的“近似模型”。大数据对于仿真分析方法也将产生重要影响,仿真将从对因果关系的分析转向对关联关系的分析,同时大数据为仿真分析也将提供新的资源和手段。另一方面,制造大数据也将成为建模仿真的重要研究对象,借助仿真技术挖掘并发挥大数据在制造各环节中的价值。此外,仿真技术还可用于大数据的筛选和预处理,大数据存储策略、迁移策略以及传输策略的优化等方面。建模与仿真和大数据将相互促进、相互补充。两者的结合将有力的促进智能制造的发展。
改编自:《智能制造概论》(作者:李培根,高亮)
相关新闻
版权声明
1、凡本网注明“来源:中国轻工业网” 的作品,版权均属于中国轻工业网,未经本网授权,任何单位及个人不得转载、摘编或以其它方式使用。已经本网授权使用作品的,应在授权范围内使用,并注明“来源:中国轻工业网”。违反上述声明者,本网将追究其相关法律责任。
2、凡本网注明 “来源:XXX(非中国轻工业网)” 的作品,均转载自其它媒体,转载目的在于信息之传播,并不代表本网赞同其观点和对其真实性负责。
3、如因作品内容、版权和其它问题需要同本网联系的,请于转载之日起30日内进行。
4、免责声明:本站信息及数据均为非营利用途,转载文章版权归信息来源网站或原作者所有。