智能制造的发展历程
2022-06-01 来源: 智造苑
随着制造业面临的竞争与挑战日益加剧,将传统的制造技术与信息技术、现代管理技术相结合的先进制造技术得到了重视和发展,先后出现计算机集成制造、敏捷制造、并行工程、大批量定制、合理化工程等相关理念和技术。
1973年美国约瑟夫·哈林顿(Joseph Harrington)博士在《Computer Integrated Manufacturing》一书中首次提出 CIM(computer integrated manufacturing)理念。它的内涵是借助计算机, 将企业中各种与制造有关的技术系统集成起来, 进而提高企业适应市场竞争的能力。其中, 特别强调: ①企业各个生产环节是不可分割的, 需要统一安排与组织——“系统的观点”;②产品制造过程实质上是信息采集、传递、加工处理的过程——“信息化的观点”;20世纪90年代,我国曾推出863/CIMS主题计划,在一些大型骨干企业尝试了计算机集成制造系统的应用。
1970年美国未来学家阿尔文·托夫(Alvin Toffler)在《Future Shock》一书中提出了一种全新的生产方式的设想:以类似于标准化和大规模生产的成本和时间,提供客户特定需求的产品和服务。1987年,斯坦·戴维斯(Start Davis)在《Future Perfect》一书中首次将这种生产方式称为大规模定制(mass customization,MC)。1993年B·约瑟夫·派恩(B·Joseph Pine II)在《大规模定制:企业竞争的新前沿》一书中写到:“大规模定制的核心是产品品种的多样化和定制化急剧增加,而不相应增加成本;范畴是个性化定制产品的大规模生产:其最大优点是提供战略优势和经济价值。”我国学者祈国宁教授认为,大规模定制是一种集企业、客户、供应商、员工和环境于一体,在系统思想指导下,用整体优化的观点,充分利用企业已有的各种资源,在标准技术、现代设计方法、信息技术和先进制造技术的支持下,根据客户的个性化需求,以大批量生产的低成本、高质量和效率提供定制产品和服务的生产方式。MC的基本思路是基于产品族零部件和产品结构的相似性、通用性,利用标准化模块化等方法降低产品的内部多样性。增加顾客可感知的外部多样性,通过产品和过程重组将产品定制生产转化或部分转化为零部件的批量生产,从而迅速向顾客提供低成本、高质量的定制产品。
20世纪90年代,信息技术突飞猛进,为重新夺回美国制造业的世界领先地位,美国政府把制造业发展战略目标瞄向21世纪。美国通用汽车公司(GM)和里海(Leigh)大学的雅柯卡(Iacocca)研究所在国防部的资助下,组织了百余家公司,由通用汽车公司、波音公司、IBM、德州仪器公司、AT&T、摩托罗拉等15家著名大公司和国防部代表共20人,历时三年,于1994年底提出了《21世纪制造企业战略》。在这份报告中,提出了既能体现国防部与工业界各自的特殊利益,又能获取共同利益的一种新的生产方式,即敏捷制造。敏捷制造的目的可概括为:“将柔性生产技术,有技术、有知识的劳动力与能够促进企业内部和企业之间合作的灵活管理(三要素)集成在一起,通过所建立的共同基础结构,对迅速改变的市场需求和市场实际做出快速响应”。从这一目标中可以看出,敏捷制造实际上主要包括三个要素:生产技术、管理和人力资源。
1988年,美国国家防御分析研究所提出了并行工程(concurrent engineering,CE)理念。并行工程是集成、并行地设计产品及其相关过程(包括制造过程和支持过程)的系统方法。这种方法要求产品开发人员在一开始就考虑产品整个生命周期从概念形成到产品报废的所有因素,包括质量、成本、进度计划和用户要求。并行工程的目标为提高质量、降低成本、缩短产品开发周期和产品上市时间。并行工程的具体做法是:在产品开发初期,组织多种职能协同工作的项目组,使有关人员从一开始就获得对新产品需求的要求和信息,积极研究涉及本部门的工作业务,并将所需要求提供给设计人员,使许多问题在开发早期就得到解决,从而保证了设计的质量,避免了大量的返工浪费。
合理化工程主要针对按订单设计(engineering-to-order,ETO)的制造企业。这类企业的产品通常需要按顾客的特殊要求进行设计制造。如果设计周期过长,导致产品交货期过长,则有可能失去顾客;如果要求在规定的时间内交货,产品设计周期过长,则产品的制作周期必须进行压缩,会影响产品的制造质量。因此对于ETO企业,压缩产品的设计周期非常重要。推进合理化工程的目的是采用先进的信息处理技术,进行产品结构的重组、产品设计开发过程的重组和设计,尽可能减少产品零部件类别,从而缩短产品研发周期,提高产品质量,缩短产品制造周期,降低产品成本,改善售后服务。
1948年诺伯特·维纳发表《控制论》,奠定了工业自动化技术发展的理论基础。自第三次工业革命以来,工业自动化技术取得了长足发展,从PLC的诞生到DCS、人机界面、PC-Based,从工业现场总线到工业以太网,从历史数据库到实时数据库,从面向流程行业的过程自动化,到面向离散制造业的工厂自动化,从单机自动化到产线的柔性自动化,从工业机器人的广泛应用到AGV和全自动立体仓库的物流自动化,工业自动化技术的蓬勃发展为智能制造奠定了坚实的基础。
从1957年Patrick Hanratty先生研发出全球第一个数控编程软件PRONTO至今,全球工业软件已经经历了60多年波澜壮阔的创新历程。众多知名的工业软件源于世界级制造企业,尤其是航空航天与汽车行业的创新实践。例如,大名鼎鼎的仿真软件Nastran就源于美国NASA,其名称的内涵就是NASA Structural Analysis;达索系统的CATIA软件则源于达索航空,而波音、麦道航空、通用电气和通用汽车也孕育了当今众多主流的工业软件。这些世界级企业在工业实践中提出的需求,成为工业软件创新的源泉。另一方面,今天广泛应用的ERP软件,发源于20世纪30年代在制造业管理实践中提出的订货点法,后来又进一步发展出物料需求计划(material requirement planning,MRP)、制造资源计划(manufacturing resources planning,MRPII),20世纪90年代,伴随着计算机系统走向C/S架构,图形界面广泛应用,Gartner提出了ERP理念,并将应用领域扩展到流程制造业。
从深刻影响全球制造业的CIM、并行工程、敏捷制造、大批量定制、合理化工程等先进理念,到工业自动化、工业软件的长足发展,以及在工业实践中蓬勃发展的工业工程和精益生产方法,成为智能制造蓬勃发展的基石。而互联网、物联网的兴起,人工智能技术的实践应用,又为智能制造理念的落地实践提供了有力支撑。
智能制造的概念经历了提出、发展和深化的不同阶段。最早在20世纪80年代,美国赖特(Paul Kenneth Wright)和伯恩(David Alan Bourne)在专著《制造智能》(Smart Manufacturing)中首次提出“通过集成知识工程、制造软件系统、机器人视觉和机器人控制来对制造技工们的技能与专家知识进行建模,以使智能机器能够在没有人工干预的情况下进行小批量生产”。在此基础上,英国Williams教授对上述定义作了更为广泛的补充,认为“集成范围还应包括贯穿制造组织内部的智能决策支持系统”。之后不久,欧、美、日等工业化发达国家围绕智能制造技术与智能制造系统开展国际合作研究。1991年,日、美、欧共同发起实施的“智能制造国际合作研究计划”中提出“智能制造系统是一种在整个制造过程中贯穿智能活动,并将这种智能活动与智能机器有机融合,将整个制造过程从订货、产品设计、生产到市场销售等各环节以柔性方式集成起来的能发挥最大生产力的先进生产系统”。
美国国家标准与技术研究院(National Institute of Standards and Technology,NIST)在《智能制造系统现行标准体系》的报告中提到,智能制造区别于其他基于技术的制造范式,是一个有着增强能力,从而面向下一代制造的目标愿景,它基于新兴的信息和通信技术,并结合了早期制造范式的特征(图1)(原文:Smart manufacturing, different from technology-based manufacturing paradigms, defines a vision of next-generation manufacturing with enhanced capabilities. It is built on emerging information and communication technologies and enabled by combining features of earlier manufacturing paradigms)。
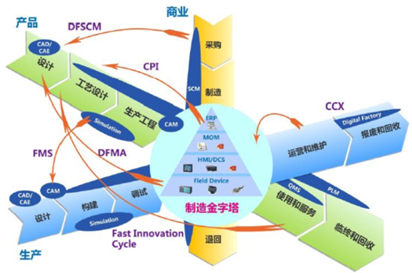
图1 美国智能制造的生态系统(来源:美国国家标准与技术研究院NIST)
我国最早的智能制造研究始于1986年,杨叔子院士开展了人工智能与制造领域中的应用研究工作。杨叔子院士认为智能制造系统是“通过智能化和集成化的手段来增强制造系统的柔性和自组织能力,提高快速响应市场需求变化的能力。”吴澄院士认为,从实用、广义角度理解智能制造,是以智能技术为代表的新一代信息技术,包括了大数据、互联网、云计算、移动技术等,以及在制造全生命周期的应用中所涉及的理论、方法、技术和应用。周济院士则认为,智能制造的发展经历数字化制造、智能制造1.0和智能制造2.0三个基本范式的制造系统逐层递进组成。智能制造1.0系统的目标是实现制造业数字化、网络化,最重要的特征是在全面数字化的基础上实现网络互联和系统集成。智能制造2.0系统的目标是实现制造业数字化、网络化、智能化,实现真正意义上的智能制造。
国家工信部在《智能制造发展规划(2016-2020年)》中定义智能制造是“基于新一代信息通信技术与先进制造技术深度融合,贯穿于设计、生产、管理、服务等制造活动的各个环节,具有自感知、自学习、自决策、自执行、自适应等功能的新型生产方式。实际上,智能制造是制造业价值链各个环节的智能化,融合了信息与通信技术、工业自动化技术、现代企业管理、先进制造技术和人工智能技术五大领域技术的全新制造模式,实现企业的生产模式、运营模式、决策模式和商业模式的创新。
目前国际上与智能制造对应术语是Smart manufacturing和Intelligent manufacturing,“Smart”被理解为具有数据采集、处理和分析的能力,能够准确执行指令、实现闭环反馈,但尚未实现自主学习、自主决策和优化提升;“Intelligent”则被理解为可以实现自主学习、自主决策和优化提升,是更高层级的智慧制造。从目前的发展来看,国际上达成的普遍共识是智能制造还处于“Smart”阶段,随着人工智能的发展与应用,未来将实现“Intelligent”。智能制造技术是计算机、工业自动化、工业软件、智能装备、工业机器人、传感器、互联网、物联网、通信技术、人工智能、虚拟现实/增强现实、增材制造、云计算,以及新材料、新工艺等相关技术蓬勃发展与交叉融合的产物。智能制造并不是一种单元技术,而是企业持续应用先进制造技术、现代企业管理,以及数字化、自动化和智能化技术,提升企业核心竞争力的综合集成技术。可以说,智能制造是一个“海纳百川”的集大成者,参见图2。
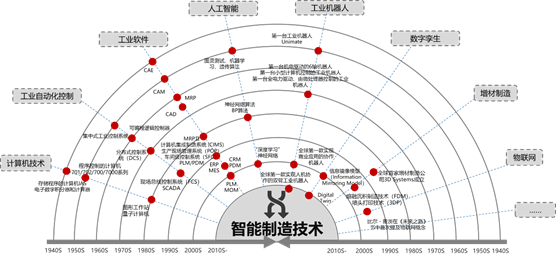
图2 智能制造技术的发展
改编自:《智能制造实践》(作者:黄培,许之颖,张荷芳)
相关新闻
版权声明
1、凡本网注明“来源:中国轻工业网” 的作品,版权均属于中国轻工业网,未经本网授权,任何单位及个人不得转载、摘编或以其它方式使用。已经本网授权使用作品的,应在授权范围内使用,并注明“来源:中国轻工业网”。违反上述声明者,本网将追究其相关法律责任。
2、凡本网注明 “来源:XXX(非中国轻工业网)” 的作品,均转载自其它媒体,转载目的在于信息之传播,并不代表本网赞同其观点和对其真实性负责。
3、如因作品内容、版权和其它问题需要同本网联系的,请于转载之日起30日内进行。
4、免责声明:本站信息及数据均为非营利用途,转载文章版权归信息来源网站或原作者所有。