【优秀案例】达威股份--清洁化高性能皮革化学品智能制造工厂
2022-04-27 来源:达威股份
编者按:
2021年,在中国轻工业联合会指导下,中国轻工业信息中心组织开展了轻工行业极具权威性和影响力的优秀案例评选活动,评选出一批轻工业创新性强、示范性好、复制性强的优秀案例。应广大企业用户的需要,在征求入选企业的意见后,我们即日起将陆续发布这些优秀案例,以助力轻工企业数字化转型。本期为第一期:《达威股份--清洁化高性能皮革化学品智能制造工厂》。
四川达威科技股份有限公司(简称“达威股份”)成立于2003年,主营业务为精细化学品的研发、生产和销售,是以皮化新材料为主业的第一家上市公司,连续5年蝉联“轻工业百强企业”“皮革十强企业”,国内市场占有率5%-6%,近年来稳居国内皮革化学品行业的龙头地位。达威股份自成立之初开始智慧办公建设,发展至今已布局了ERP\OA\MES\WMS等自动化软件,并且建立了大数据中心。
背景与趋势:
皮革化学品是皮革行业的一个主要配套行业。我国专业皮革化学品的年需求量在80万吨~100万吨,市场销售总额在100~150亿元。虽然,近20年来国内皮革化学品生产技术取得了很大的进步,但目前国内皮革化工企业还没有一家智能化工厂,基于工艺水平的限制,国内产品的性能和稳定性等方面尚难满足高档皮革产品的需要,主要使用在中低档市场。
“十四五”的大幕已然开启,皮革行业要立足中国现代化发展新目标和以国内大循环为主体的“双循环”发展新格局,坚持以科技自主创新和产业结构调整为核心引领,强化产业基础,优化产业体系,适应新形势,谋求新突破,跨入新征程,实现新发展。《皮革行业“十四五”高质量发展指导意见》提出以科技创新、质量标准、绿色低碳、“三品””战略、推动行业实现高质量发展,指出了我国皮革行业后续发展重点方向之一是绿色制造、降本增效。
达威股份是皮革新材料全品类制造型企业,属于多品种、小批量的流程型精细化工,生产线涵盖400多种产品,生产原材料有几百种,且单个产品的产量并不大,需要根据生产计划不断切换生产线的生产任务。过程中就涉及反应装备的清洗、工艺变更、原料变更、检测方法更改等一系列流程,故而带来了生产效率低下、加急订单插入困难,由此引发了成品库存积压、原料备货计划不准确等更多问题。目前国内皮化生产厂商大多仅能实现半自动生产,称量加料、反应进程监测、升降温等工序仍由人工手工完成,成品质量对工艺员的个人技术水平的依赖性高,人的疲劳、情绪、压力等都会使产品质量(尤其是工艺要求高的产品)产生波动。上述种种问题,是国内皮化生产厂商的普遍痛点,故而生产过程的智能化升级非常必要!
制造业成本最高的是原材料成本,2017年达威股份新津老厂的运营成本中,原料成本高达80.77%,优化反应工艺、减少过程控制不力带来的原材料报废等就显得尤为重要。除了原料成本,人力成本也很高,同样以2017年为例,新津老厂人力成本占据2.2%,而也就是说除了原料成本外,人力成本占据了生产成本的大部分,增加单位人次的产值也是个重要的优化方向。在制造业利润被不断压缩的今天,降低生产成本非常迫切,所以本项目的建设很迫切。如巴斯夫、朗盛等,在工业4.0的推动下进行生产线智能化改造,实现了生产、检测、包装的全自动化。智能化生产线的投产大大缩短了生产时间、缩减了人力成本,降低了生产成本。以巴斯夫德国工厂为例,每个生产车间都设置了一个中央控制室,日常生产活动中仅在中央控制室配置了人员,加料、出釜、包装等工序均由控制室根据生产流程发出指令,车间中除了配备一些巡检人员外,不再配备操作工人。
建设内容:
2017年,达威股份在天府智能制造产业园的清洁化皮革化学品智能化生产工厂(后文简称“达威智能工厂”)启动,占地面积100亩,斥资3.12亿元,项目于2019年年底正式投产。项目技术方案立足于清洁化皮革化工材料的生产需求,整合皮革行业和工业信息化领域的顶尖院校、龙头企业(四川大学、浙江中控、用友软件)等一流资源,组成联合项目开发共同体,以达威股份内部网络硬件、软环境为支撑进行数字化建模,构建数据信息统一共享平台,形成覆盖全厂的高效安全、信息共享、智能化、现代化的“数字化企业”支撑体系。
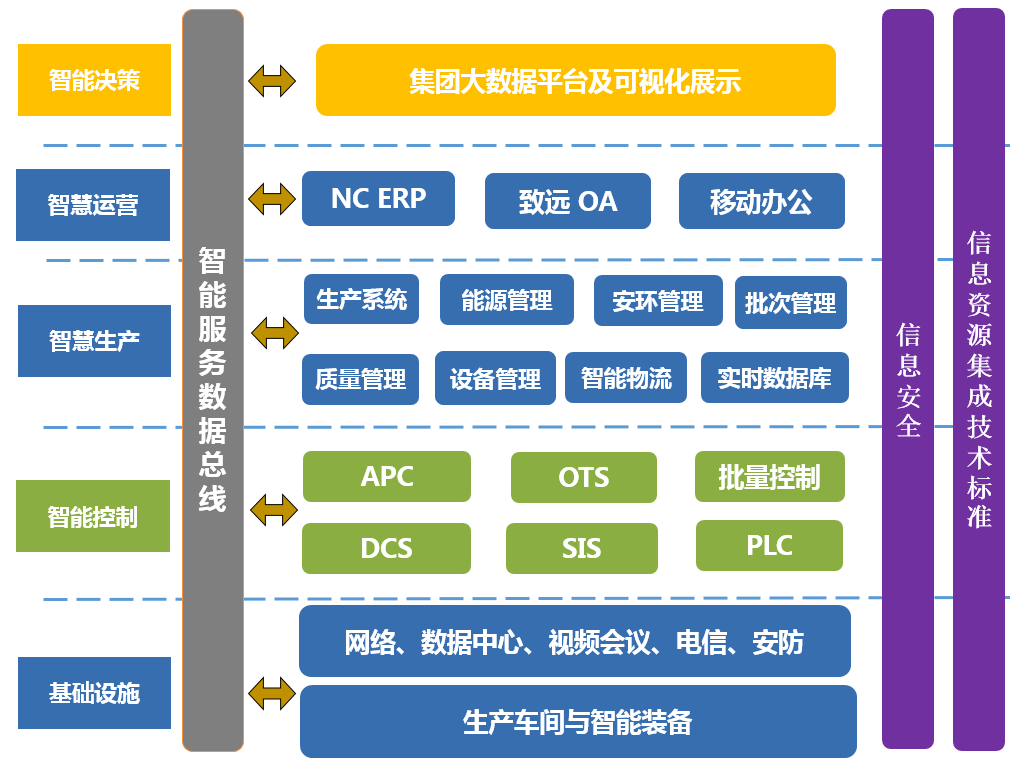
图1 智能工厂整体架构
(一)整体架构
达威智能工厂的生产管理体系,从现场装置到集散控制系统(DCS)、安全连锁系统(SIS)、配方管理系统(VXBatch)、到生产管理层MES业务,再到企业经营层ERP系统的集成实现从底层到上层的真正的管控一体化的信息化系统。
整体网络架构从上往下,可分为三层:企业经营层、生产管理层、智能控制层。
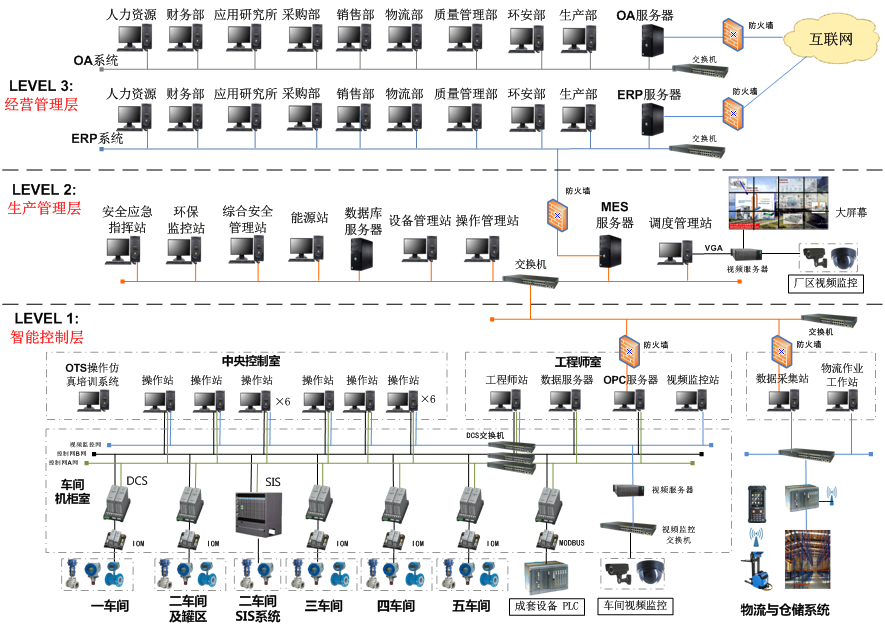
图2 智能工厂通讯网络架构
达威智能工厂建设了5个数字化生产车间,涉及以下生产线:加脂剂生产线;氯磺化、硝化棉生产及中试生产线;复鞣剂生产线及酶制剂;料膏、助剂生产线;丙烯酸、聚氨酯生产线等。
成品库采用四向车密集仓储系统,层数为4层,整体规划8台四向车,4台垂直输送机,四向车可实现换层运行。采用先进的重型四向穿梭车、托盘垂直输送机、托盘输送机、穿梭式货架等硬件设备,方案中规划储存货架数量为7688个货位,可实现全自动出入库。引入WMS仓储管理软件和WCS监控软件,应急状态可在WCS 系统或者现场ECS操作屏实现出入库操作(需补录出入库信息)。托盘标签采用条形码进行信息管理。入库前需设计有外形尺寸检测和称重装置,确保货物安全入库。WCS系统通过与ERP系统的数据接口链接供应链,共同建设智能化仓库,实现物流系统的智能化。
![]() |
图3 仓储物流系统运行架构
DCS集散控制系统、Batch配方管理系统通过MES生产管理系统发出的生产指令进行工作。Batch系统自动采集数据,将生产过程中反应进程、技术指标、设备状态等数据传输给MES系统;DCS集散控制系统通过反应釜传感器采集的技术参数进行过程判定,根据配方自动控温、自动加料,如有异常情况将报警信号传输给中控室,如果遇到紧急情况,SIS系统将自动介入,执行卸压,关停进料等停车操作,保证工厂本质安全。MES生产管理系统通过与ERP系统的数据接口链接供应链,根据库存情况发出排产预警和发送原材料需求数据给采购部。
(二)系统功能
达威股份大数据平台的建立,通过打通NCERP企业运营管理系统与各个信息化系统的接口,连通生产控制软件(如DCS/Batch/MES)、物流管理系统、OA办公系统的数据,信息通道互联互通以实现工业化和信息化的深度融合。ERP系统采集客户订单数据传送给MES系统,MES系统制定生产计划, VxBatch系统调取工艺单,配合DCS系统实施生产控制。生产过程中的原料称重、物料输送、在线监测、成品包装入库等全程高度自动化、机械化,基本不需要生产操作工人,生产管理员在中控室,通过VxBatch系统采集的数据传输给DCS系统控制生产流程,现场工作人员以巡检巡视为主。人工的需求主要集中在标准工艺制定和改进、生产数据分析、自动化模式优化等方面,MES系统的应用除去大量重复人工计算和分析工作,提升了员工的劳动价值。高度的自动化避免了人工操作的不稳定性,提高生产效率、提升产品合格率;同时生产人员大幅减少接触化学原料、粉尘等恶劣操作环境的机会,职业病的几率可大幅度降低,减少劳务纠纷。
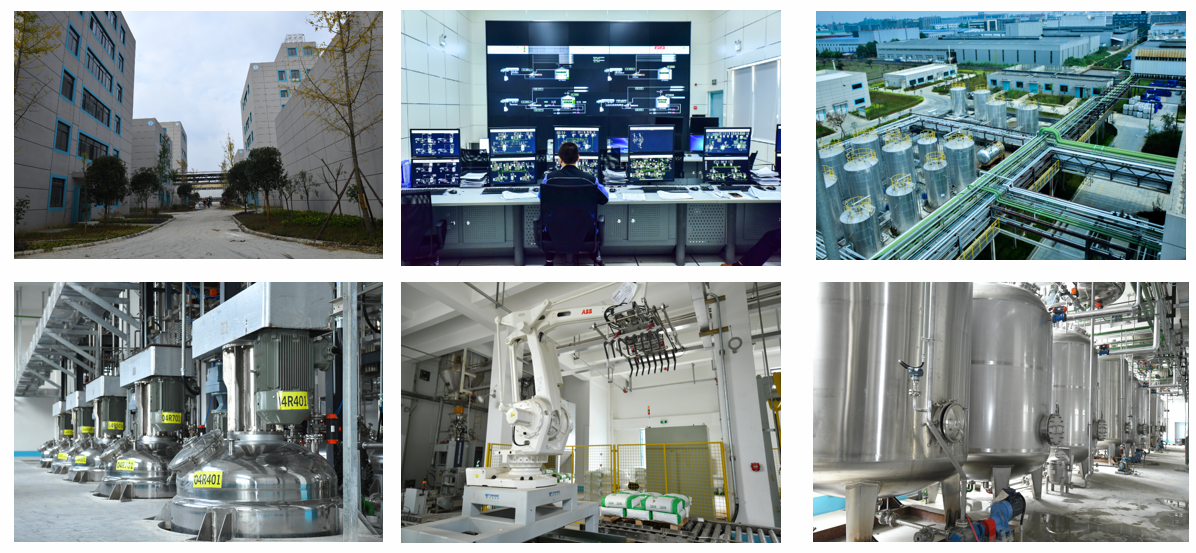
图4 智能工厂实拍图
(三)安全部署
智能化进程中,信息安全至关重要。我公司部署的服务器支持数据库自动备份、各地虚拟化集群远程容灾技术,采用Zabbix监控平台,通过能监视各种网络参数,保证服务器系统的安全运营,保证在硬件与网络方面的数据安全,也保证了在出现极端灾难事故时系统的快速恢复能力。除了诸如账号管理、登录管理、功能权限等一般系统常见的安全措施外,先进的数据权限可以保证系统进行数据行级的增、删、读、改等操作进行控制,避免了用户对不属于授权范围数据进行非法地访问。为了长期安全存储数据,公司配置了企业级的数据存储系统。为了降低网络安全带来的风险,公司设置了华为防火墙、信息传输管理系统,对公司内部实现了统一管理计算平台,全方位对内到外,保障公司的计算机数据及系统的安全。
应用成效:
达威智能工厂的中央控制室更加优于巴斯夫德国工业4.0工厂,全厂仅配置一个中央控制室,可监控和控制5个数字化车间。通过对产品类型的区分,生产线分为了粉剂产线和液体产线;粉剂产线配备自动包装机器人,粉剂产品出线后自动包装和码垛,由物流穿梭车运送到成品库,在WMS仓储管理系统的指挥下二维码扫描入库;液体车间生产产品由成品储罐经管道直接输送到成品库,在成品库进行自动灌装并扫码入库。所有单体材料存储在原料罐区,在MSE系统生产指令下达后根据工艺通过专用管道自动输送到生产车间,通过Batch配方管理系统管控添加方式。综上,原材料输送、加料、包装等基本不再需要人工操作。通过使用传感器、DCS系统、MES系统等手段,在物料添加、过程控制和设备管理等环节实现了自动化、智能化管控,解决了人员依赖问题;进而排除了生产过程中存在的安全隐患和原料泄漏风险。
达威智能工厂自2019年7月开始投产运行,故以投产后一年、即2020年(2020年产量为剔除疫情影响,取值为2020年7月至2021年6月数据)的相关指标,与达威股份新津老厂2019年的运行数据进行对比和分析。
(1)生产效率:2020年智能工厂产值为39909万元,生产线配置65名生产人员(含一线管理人员和生产工人),人均产值为614/万元;2019年老厂产值为27215万元,生产线配置63名生产人员,人均产值为432/万元;综上,生产效率提升42%。
(2)2020年智能工厂产品销售收入为42400万元,生产运营费用为2088万元,每万元销售额的运营费用为492元;2019年老厂产品销售收入为32305万元,生产运营费用为1994万元,每万元销售额的运营费用为617元;综上,运营成本减低20.3%。
(3)能耗:2020年智能工厂产值为39909万元,工厂生产能耗(水电气)费用为3608887元,每万元产值耗能90.4元;2019年老厂产值为27215万元,工厂生产能耗(水电气)费用为3494932元,每万元产值耗能128.4元;综上,生产效率提升29.6%。
由上述估算,清洁化高性能皮革化学品智能工厂项目投产后,可达到生产效率提高40%以上,运营成本降低20%以上,单位产值能耗降低20%以上。
(备注:①上述数据包含集团内部交易;②生产运营费用不包含新增资产的折旧摊销。)
专家点评:
清洁化皮革化学品智能化生产工厂利用网络和通讯技术实现数据互联互通,将企业信息化系统(DCS系统、SIS系统、VxBatch系统、MES 系统、ERP系统)进行业务集成,打通企业业务流和信息流,改进了部门之间信息传递效率,是企业实现管控一体化的基础,同时也开启了高等院校、系统集成商、用户的合作新模式。为皮革化学品制造行业大大地减少劳动用工,降低劳动强度,提高自动化程度,降低单位产品耗,形成工业化生产的规模效应。
相关新闻
版权声明
1、凡本网注明“来源:中国轻工业网” 的作品,版权均属于中国轻工业网,未经本网授权,任何单位及个人不得转载、摘编或以其它方式使用。已经本网授权使用作品的,应在授权范围内使用,并注明“来源:中国轻工业网”。违反上述声明者,本网将追究其相关法律责任。
2、凡本网注明 “来源:XXX(非中国轻工业网)” 的作品,均转载自其它媒体,转载目的在于信息之传播,并不代表本网赞同其观点和对其真实性负责。
3、如因作品内容、版权和其它问题需要同本网联系的,请于转载之日起30日内进行。
4、免责声明:本站信息及数据均为非营利用途,转载文章版权归信息来源网站或原作者所有。