虚拟制造+数字孪生发展及应用实践
2023-08-29 来源:自动化仪表
1 研究背景与发展现状
虚拟制造系统首先要感知、建模,再进行分析推理。数字孪生是虚拟制造的使能技术。如果没有数字孪生对现实生产体系的准确模型化描述,所谓的虚拟制造系统就是无源之水,无法落实。一方面,数字孪生可以支撑制造的物理世界和信息世界之间的虚实映射和双向互动,进而形成数据感知-实时分析-智能决策-精准执行的智能闭环。另一方面,数字孪生可以将实际的运行状态、环境变化、突发扰动等参数与信息空间数据(如仿真预测、统计分析、领域知识等)进行充分的互动和深度融合,以提高制造过程中物理世界和信息世界的同步性和一致性。数字孪生与虚拟制造的关系如图1所示。
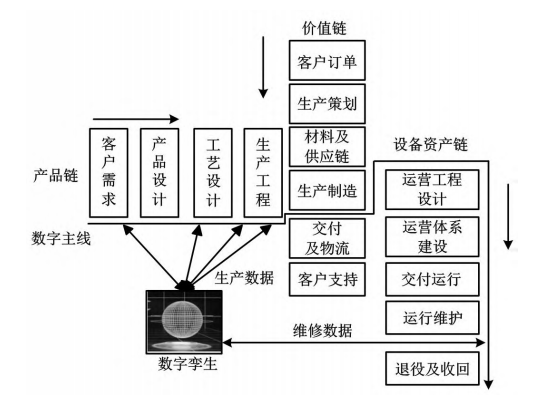
1.1 虚拟制造
虚拟制造以虚拟现实(virtual reality,VR)和仿真技术为基础,对产品的设计、生产过程统一建模,在计算机上实现产品的设计、加工和装配、检验、使用,从而完成整个产品生命周期的模拟和仿真。虚拟制造技术近年来受到广泛关注。该技术利用计算机仿真技术模拟产品设计、制造和生产过程,帮助企业优化生产流程、提高产品设计精度和生产效率。随着科技的发展,虚拟制造技术已经结合了许多相关技术,如云计算、人工智能、物联网等,以提供更多的应用场景和实时数据支持。
多领域、多尺度融合建模是虚拟制造的关键技术之一。通过建立多领域、多尺度的模型,可以对不同的制造过程进行有效的仿真和优化,从而提高制造效率和产品质量。数据采集与传输是虚拟制造的基础,涉及数据的实时采集和传输,需要结合各种传感器和通信技术。全周期数据管理是虚拟制造的另一项核心技术,包括数据的收集、存储、分析和应用。通过全周期数据管理,可以实现对生产过程的全面监控和优化。数据驱动与物理状态融合的状态评估是虚拟制造的关键技术之一,通过将实时数据与模型进行融合,可以实现对生产状态的评估和预测。VR呈现技术是虚拟制造的重要组成部分。该技术通过将数字化的制造过程和产品呈现为视觉化场景,为制造过程提供直观的展示。高性能计算技术是虚拟制造的关键技术之一,可以提供高速的计算和数据处理能力,支持复杂的虚拟仿真和优化。这些技术的发展和应用将促进制造业的数字化转型和智能化升级。
1.2 数字孪生
数字孪生是充分利用多种数据(包括物理模型、传感器、运行历史、试验信息等),集成多学科、多物理量、多尺度、多概率的仿真过程。其在虚拟空间中完成映射,从而反映相对应的实体装备全生命周期过程。数字孪生技术的实现离不开许多先进技术的发展和应用。其技术体系按照从基础数据采集层到顶层应用层的顺序可以被划分成四个层次,分别是数据保障层、建模计算层、数字孪生功能层和沉浸式体验层。每一层功能的实现都在前一层的基础之上进行,都是对前面各层功能的进一步丰富和拓展。
数字孪生的关键技术有多领域多尺度融合建模、数据驱动与物理模型融合的状态评估、数据采集和传输、全寿命周期数据管理、VR呈现等。其中,多领域多尺度融合建模与虚拟制造中的建模关键技术一致。在具有复杂机理结构的数字孪生目标系统中,通常很难构建准确、可靠的系统级物理模型。因此,仅仅使用目标系统的解析物理模型对数字孪生目标系统进行状态评估,并不能取得良好的评估效果。数字孪生技术使用数据驱动的方式,利用系统的历史和实时运行数据对物理模型展开更新、修改、连接和补充。数字孪生对系统机理特征和运行数据特征进行了充分的融合,使之可以与系统的实时运行状态更好地结合,从而得到一套可以动态、实时地跟踪目标系统状态的评估系统。数字孪生系统是物理实体系统的实时动态超现实映射。数据的实时采集传输和更新对于数字孪生具有至关重要的作用。在数字孪生系统中,数量众多、种类繁多的高精度传感器作为核心,构成了数字孪生系统的感知基础。要实现全生命周期的数据存储和管理,就必须借助服务器的分布和冗余的存储。因为数字孪生系统对数据的实时性有非常高的要求,所以要对数据的分布架构、存储方式和检索方式进行优化,从而得到实时、可靠的数据读取性能。这就是数字孪生系统所面临的挑战。VR技术可以让用户快速掌握系统的工作原理、结构、特征、变化趋势、健康状况等多方面信息,从而激发用户对系统的优化与创新。在当前的云计算环境下,优化可以从两个方面着手,即云计算环境下的高性能数据分析算法的云端化和异构加速架构。数字孪生与虚拟制造的对比如表1所示。

工业4.0指由人工智能、物联网、机器人技术、无人机、无人驾驶汽车、VR等主导的新一代工业革命。虚拟制造与数字孪生是工业4.0的必备技术。目前,国内外正在进行各种类型的数字孪生研究。德国西门子开发了模拟本公司生产设施的数字孪生系统,以构建智能工厂。得益于此,西门子在工厂作业效率和质量改进方面取得了显著成效。智能工厂通过安装在工厂和机器中的传感器实时收集和分析数据,能够快速了解工厂情况并通过分析实现自行控制。日本三菱重工在建造风力发电厂的过程中引入了数字孪生的概念。数字孪生帮助三菱重工通过考虑风向、风速和地形来选择发电厂的最佳位置。此外,新加坡政府还将整个城市数字化,并将数字化用于预测和管理交通。荷兰鹿特丹市正在实时收集和分析船舶运营信息,以升级港口物流系统。
数字孪生不仅应用于制造业,在医疗、能源、金融和公共服务等领域都得到了广泛应用。未来,数字孪生有望通过与人工智能相结合,演变成更智能的形式。数字孪生的应用范围覆盖将更大,而虚拟制造将成为制造业不可或缺的一环。
2 研究开发与应用实践
虚拟制造和数字孪生技术的发展,为工业4.0提供了强有力的支持。将生产线上的物理过程数字化,为智能制造提供了强有力的技术支持。例如,在工业机器人领域,通过使用虚拟制造和数字孪生技术,可以实现机器人的智能化控制和自适应,从而提高生产效率和产品质量。此外,虚拟制造和数字孪生技术的应用还可以支持在产品生命周期的各个阶段中,实现产品的数字化设计、制造和维护。
2.1 基于虚拟制造的虚拟油管监测系统
虚拟油管监测系统需要能够准确地模拟油管监测的真实环境,包括管道结构、流体传输、温度、压力等参数。这样可以帮助操作人员更好地理解和分析实际油管的运行情况。本小节设计的基于虚拟制造的虚拟油管监测系统应用于某钢厂中小型车间。根据需求,该系统先对VR的交互功能进行研究,再采用ActiveX技术把基于VR的测控界面封装成标准化控件嵌入到组态软件中,以实现物理油罐与虚拟油罐的无缝链接和动态数据交换,最终实现远程监测。
基于虚拟制造的虚拟油管监测系统通过建模仿真技术与软件开发技术,实现虚拟人机交互,并通过运用几何建模、物理建模、运动建模、行为建模、交互映射与模型分割等实现实时仿真。该系统通过软硬件相结合的设计,实现虚拟场景的构建与仿真。虚拟场景的设计包括可视化、数据处理和用户交互等。虚拟场景设计结构如图2所示。
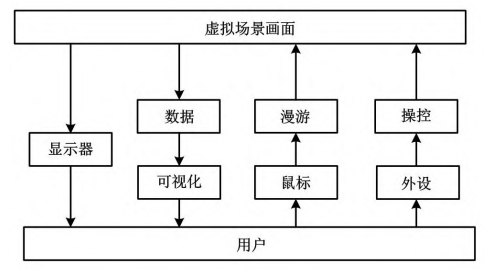
图2 虚拟场景设计结构图
基于虚拟制造的虚拟油管监测系统运用多传感器数据融合技术及模糊控制技术,实现油罐监控。虚拟油罐平台的功能包括系统主画面、历史曲线权限设置、操作系统、智能报警以及网络浏览。智能测控机理为传感器采集油位数据。数据先传输到数据融合模块,再传输到总控平台以输出信号。智能测控机理如图 3所示。
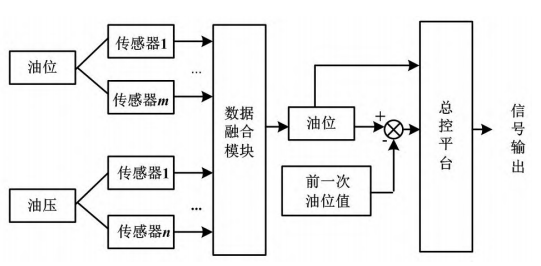
图 3 智能测控机理
地下油库虚实场景如图 4 所示。
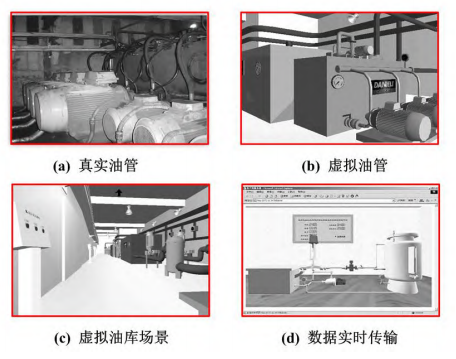
图 4 地下油库虚实场景
本文根据如图 4( a) 所示的真实油管现场实际环境搭建虚拟环境。虚拟油管如图 4( b) 所示。虚拟油管监测系统实现了如图 4( d) 所示的数据实时传输与虚拟人机交互,最终实现操作人员的远程智能测控。图 4( c) 为应用基地实际场景与虚拟监控画面。
2.2 智能农业温室微环境监测系统
智能农业温室微环境监测系统应具备温度、湿度、光照、CO2 浓度、pH 值、土壤营养、病虫害等参数的监测功能,并能进行数据记录、分析、警报和远程监控,以实现高效的农业生产和资源管理。基于虚拟制造的智能农业温室微环境监测系统的功能如下。首先,通过农业智能巡视机器人在温室内进行自主行走,完成所需大棚内数据信息的采集。然后,温室环境网络化监测系统平台远程获取温室内机器人采集到的微环境数据,并实时显示在远程界面以供监测。接着,作物生长环境专家系统实现基于智能机器人与监测平台的、面向作物生长过程温室监控的辅助决策功能。最后,系统在某农业基地 840 m2 温室番茄种植区完成现场验证。虚拟温室模型如图 5 所示。
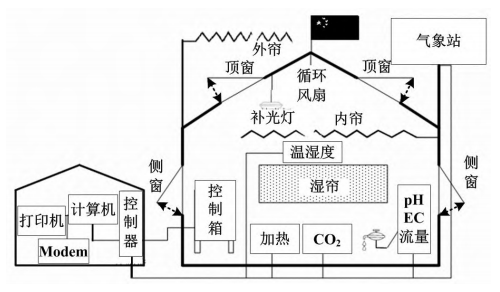
图 5 虚拟温室模型
因为从农业物联网平台中获取到的数据非常庞大,而系统生成的信息非常复杂,所以仅依靠农户的技术水平很难直接使用这些原始数据进行决策。农业专家只能根据定量分析的结果来作出正确的判断和决策。也就是说,数据采集和控制设备的作用非常有限。解决问题的关键是对传感器获取的大量信息进行及时处理和整合。解决方案之一是在每个农场都建一个计算机中心。但该方案的可行性太低。解决方案之二是把这些数据存储在云中,从而为以后监测作物的生长环境和生长过程,以及食品安全追溯等活动提供证据和奠定基础。目前,在云服务端上已完成数据采集、统计以及对温室设备的远程控制服务等,并为将来的发展预留了适宜的接口。这将便于今后在这些服务的基础上进一步衍生出更多的农业生产服务,如植物生长过程分析、农业专家系统以及农业数据挖掘服务等。
温室微环境监测系统可实现以下功能。
①数据采集。湿室微环境监测系统可采集温室大棚的各种影响因素的数据,如温湿度、光照、CO2 浓度、土壤水分和温度等信息。
②专家系统。作物生长环境专家系统实现基于智能机器人与监测平台的面向作物生长过程温室监控的辅助决策功能。整个基于虚拟制造的温室微环境监测系统结构如图 6所示。
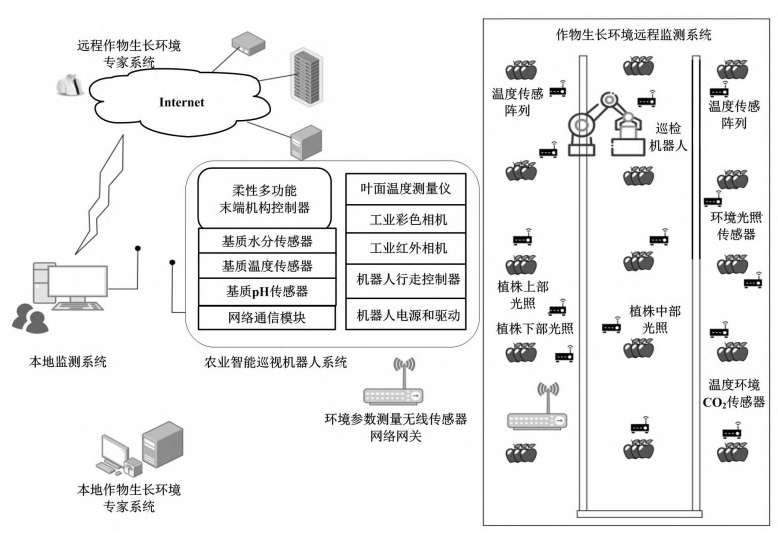
图 6 温室微环境监测系统结构图
③通过农业监测机器人采集数据,可以实现数据的精准性、实时性、一致性。借助监测平台的智能分析能力,可以摆脱温室控制对人的依赖。温室虚实场景如图 7 所示。
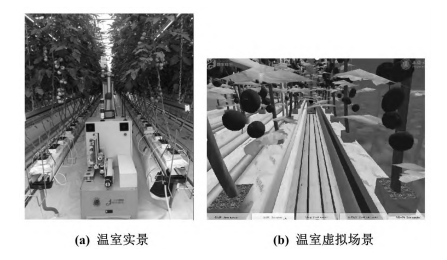
图 7 温室虚实场景
智能农业温室微环境监测系统的应用可以提高农业生产的质量和效率、减少资源浪费,同时也为农民提供了更便捷、可靠的农业管理工具。
2.3 虚拟锂电池化成试验生产线
虚拟锂电池化成试验生产线的应用需求包括工艺优化、质量控制、过程仿真、培训和技能提升,以及可视化和决策支持等。虚拟系统可以帮助锂电池制造企业提高生产效率、优化质量管理,并降低成本和风险。虚拟系统设计需针对日产量为 10 000 片、容量为 10 Ah 的锂电池的生产过程。虚拟仿真过程按照生产工艺要求,采用集运箱方式运输锂电池; 采用流水线方式进行虚拟仿真,并需要对集运箱和电池导体模型进行两级编码。虚拟仿真中的氮气作为消防媒介,将现场总线与工业以太网结合。这将有助于优化生产过程、提高效率和安全性。虚拟生产线是实现了工位控制、现场工作站控制和系统集控的大系统,可通过虚拟仪表对数据进行显示和采集仿真模拟。虚拟系统需设计开放式的系统数据库,以便实现系统数据的实时共享。
虚拟制造技术应用于生产体,可以实现对物流控制、仓储管理、过程控制和工艺参数控制的模拟。
虚拟系统通过虚拟制造技术,在仿真界面全面满足锂电池生产工艺要求; 通过虚拟仿真,优化生产过程占地面积,提高现实场地使用效率; 通过模拟仿真,确保工艺流程的完整性、可实现性、可靠性。模拟仿真要同时保证自动化过程与紧急状态下人工干预的可实现性。仿真过程需同时满足消防要求,以确保安全生产。
自动化生产的工位布置如图 8 所示。
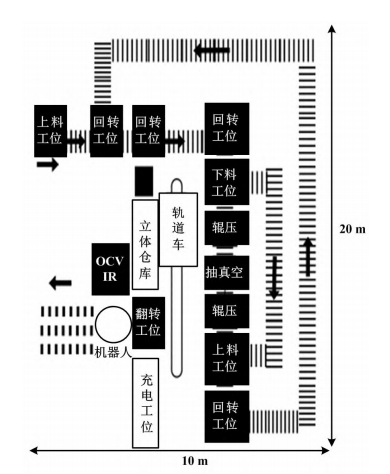
图 8 工位布置平面图
锂电池化成试验生产线部分虚拟场景如图9所示。
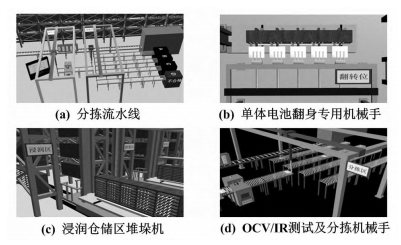
图 9 生产线部分虚拟场景
虚拟锂电池化成试验生产线的应用可以帮助优化生产线设计、改进工艺、提升操作员技能,并提供故障诊断和优化的支持。虚拟化技术在锂电池生产领域的应用正在逐渐增加,可以提高生产效率、降低成本和改善产品质量。
3 发展趋势
①更高级的仿真技术。虚拟制造和数字孪生将更加强调仿真技术的发展,包括物理仿真、运动仿真、流体仿真等,以提供更真实、准确的模拟环境。这将帮助制造企业在产品设计、工艺规划和生产过程中进行更精确的分析和优化,从而减少试错成本和时间。
②深度学习和人工智能的应用。虚拟制造和数字孪生技术将与深度学习和人工智能技术结合,以实现更智能化的生产过程。通过分析大数据、学习和预测模式,该技术可以提供更精确的预测和决策支持,帮助企业优化生产计划、改进质量控制和降低故障率。
③跨领域整合。虚拟制造和数字孪生将在不同领域之间进行更紧密的整合,包括工程设计、制造、供应链管理等。通过虚拟制造和数字孪生技术,企业可以在产品生命周期的不同阶段进行信息传递和共享,以实现多领域的协同工作。
④物联网的融合。虚拟制造和数字孪生将与物联网技术相结合,实现设备和系统之间的互联互通。通过物联网的数据采集和传输,企业可以实时监控设备状态、收集生产数据。通过将设备状态与数字孪生模型进行对比分析,可以实现远程监控、预测维护和智能调度。
⑤增强现实和VR应用。虚拟制造和数字孪生将借助增强现实和 VR 技术,为制造业提供更直观、沉浸式的体验。通过增强现实和 VR 技术,企业可以在虚拟环境中进行产品设计、工艺规划和培训,从而提高效率和质量。
4 结论
虚拟制造借助增强现实和 VR 技术,可以提供更直观、沉浸式的体验。数字孪生与物联网技术的结合可实现设备和系统的互联互通,可实时监控设备状态、收集生产数据,实现物理世界的精准映射。虚拟制造和数字孪生已经在油管检测、农业温室及锂电池化成试验生产线中取得显著的进展和良好的应用实践效果。未来,虚拟制造和数字孪生的发展将更加注重仿真技术的提升、深度学习和人工智能的应用、跨领域整合、物联网的融合以及增强现实和 VR 技术的应用。数字孪生驱动虚拟制造将打造具有超高并发基础设施、全面价值交付体系和三元空间生态环境的元宇宙。
原文刊载于《自动化仪表》2023 年 8 月 作者:上海大学机电工程与自动化学院 熊瑶 费敏锐
相关新闻
版权声明
1、凡本网注明“来源:中国轻工业网” 的作品,版权均属于中国轻工业网,未经本网授权,任何单位及个人不得转载、摘编或以其它方式使用。已经本网授权使用作品的,应在授权范围内使用,并注明“来源:中国轻工业网”。违反上述声明者,本网将追究其相关法律责任。
2、凡本网注明 “来源:XXX(非中国轻工业网)” 的作品,均转载自其它媒体,转载目的在于信息之传播,并不代表本网赞同其观点和对其真实性负责。
3、如因作品内容、版权和其它问题需要同本网联系的,请于转载之日起30日内进行。